Static rope with integrated cut resistance. This means high-strength aramid fibers are integrated into the rope sheath during the braiding process. As a result, the INTERSTATIC PROTECT has almost double the cut resistance compared to a static rope with a comparable sheath proportion and diameter. These characteristics, together with its low elongation values, make the INTERSTATIC PROTECT the first choice for all applications when the rope is exposed to sharp edges or whenever an additional safety margin is desirable.
-
Description
-
Features
- Thermo Shield treatment for pleasant handling
- Tracer threads in the rope sheath indicate the rope diameter
- Increased cut resistance through the integration of aramid fibers into the rope sheath
- Caution: the rope does not eliminate the need for adequate edge protection
- Tested for use with ActSafe model ACC (applies to diameter 11.0 mm in color night)
-
Technical information
- Core proportion: 56 %
- Diameter: 11 mm
- Knotability: 1,10
- Sheath proportion: 44 %
- Schrinkage H20: 2,40 %
- Weight per meter: 77 g/m
- Minimum breaking strength: 35 kN
- Static elongation: 2 %
- Minimum breaking strength in figure-of-eight knot: 20 kN
- Certification: EN 1891 Typ A
- Material: Polyamid/Aramid
- Rope Type: Static A
-
EDELRID technologies
-
PDF downloads
-
Safety instructions & manufacturer information
- This product is part of personal protective equipment (PPE) and/or warnings and safety information are available for this product. Please refer to the instructions for use.
- Manufacturer: EDELRID GmbH & Co. KG | Achener Weg 66 | 88316 Isny i. A. | Germany | www.edelrid.com
World First in the Static Rope Sector: Reinforced by Aramid Fibers
The INTERSTATIC PROTECT is a real world first in the static rope sector. In a special braiding process, high-strength aramid fibres are braided into the rope sheath. Compared to polyester or polyamide, aramid has a significantly higher cut resistance. The result is a static rope with almost twice the cut resistance of ropes with comparable sheath content and diameter.
In the construction, we rely on dimensionally stable core yarns in combination with a fanned sheath. This combination ensures high breaking values, minimal shrinkage and low elongation behaviour under load. At the same time, thanks to the Thermo Shield treatment, the rope remains pleasantly soft to handle, making it easy to use with all abseiling and rescue equipment.
Sheath
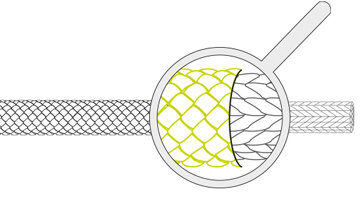
Plied:
In this process, the yarns are wound in parallel on bobbins without twisting. Because the fibres are processed in parallel, maximum fibre utilisation is achieved and the technical values in terms of maximum breaking forces are the highest achievable. The only disadvantage is the somewhat lower abrasion resistance than with twisted constructions.
Core
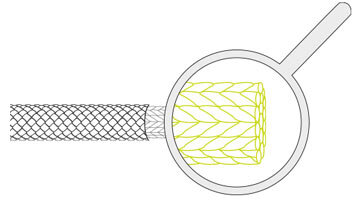
Twisted:
The standard process for making core inserts. Depending on the respective construction, 3 basic twists (possibly 5 or 6) are twisted to form a core. In static ropes, 13 - 22 of these core plies form the load-bearing core.