These long textile bonds we call ropes have come a long way. Probably since humans seriously started climbing their surrounding mountains ropes have been one of the most efficient ways to secure climbers from their exposure to falling. From the early days of handmade natural fibers based ropes, the revolutionary introduction of synthetic fibers and their first use in ropes in the 1940s and 1950s to the invention of the Kernmantle construction in 1953 by EDELRID – textile ropes for all types of climbing have evolved to a technical level where it is almost impossible in a real life scenario for a rope to fail due to overload.
THE URGENT NEED TO MEASURE CUT RESISTANCE OF ROPES:
The motivation
However, every year accidents with severed ropes are recorded and climbers get hurt or, given the usual vertical exposure of our sport, die. So the question is: why does this happen? One of the - if not the first to document and analyze accidents caused by severed ropes was safety research pioneer Pit Schubert in the 1960s. Later the German alpine club (DAV) continued his work [1]. In the below statistics we put together all known accidents caused by severed ropes in a climbing scenario merging the DAV statistics with documented accidents by the American Alpine Journal[2] as well as other accidents known to EDELRID.
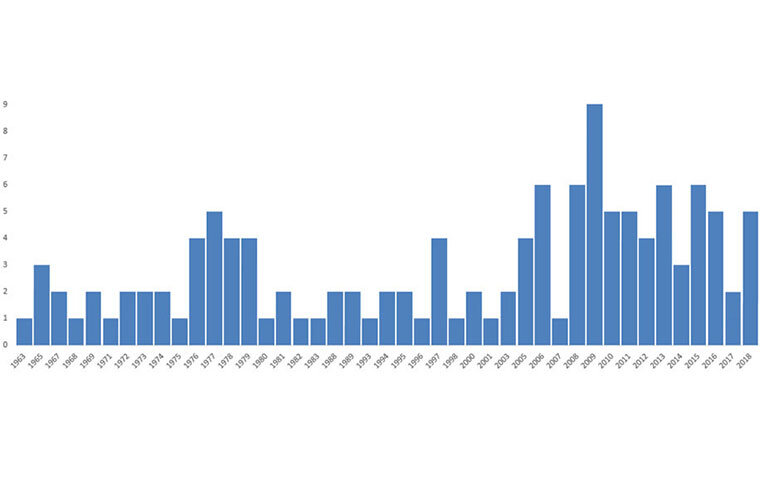
Since 1963 this accumulates to 128 documented accidents (42 of them known to be fatal). Including 2018 this means an average of about two accidents per year. However, the bigger question that arises from this is obviously: What caused these accidents? Unfortunately, not all accidents are documented well and causes are not always known. But given the information that is available, we see that the main three causes are:
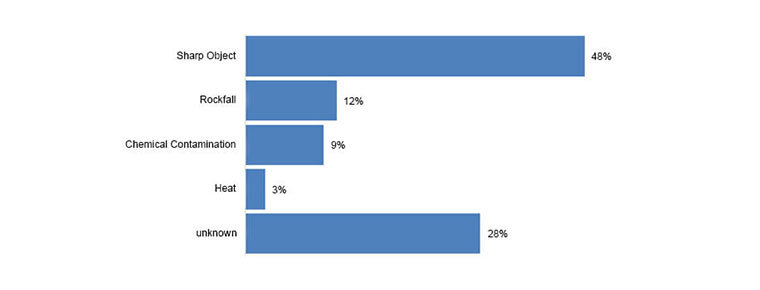
The number one cause for accidents where ropes fail is due to sharp objects. This category contains everything from sharp edges (over 60 %) to sharp carabiners (approx. 17 %) to sharp teeth of rope clamps (10 %).
But if the biggest danger for today's (and yesterday's) ropes are sharp edges why didn't manufacturers try to improve on the cut resistance of their ropes? The answer is quite simple and frustrating at the same time: Because there hasn't been a reliable way to measure cut resistance! And if there isn't a method to measure how well a rope persists a load over a sharp edge how are you able to tell whether you achieved exactly this.
Now admittedly this is not a new idea. In the following we would like to describe a few attempts from the past that set out to measure the cut resistance of ropes and the crucial problem that they all faced.
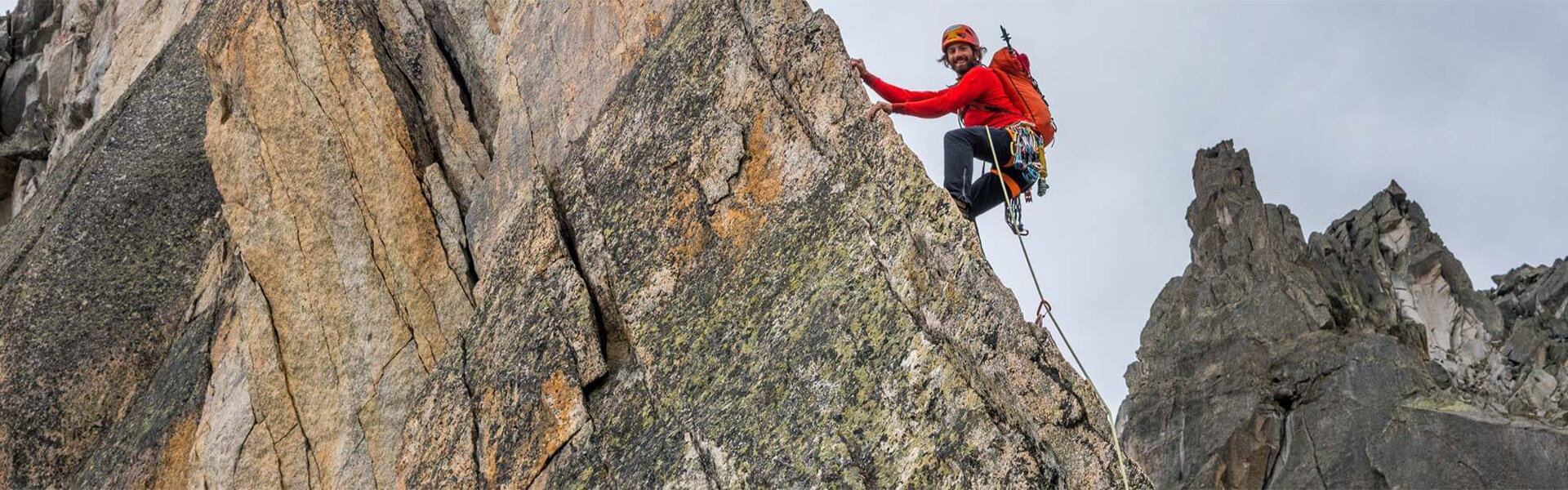
2002: UIAA 108 – Sharp Edge Test
In 2002 the UIAA introduced a standardized test method to identify and mark "cut resistant ropes". The test was based on the standard drop test described in the European standard for dynamic ropes EN 892 or the UIAA 101 standard for dynamic ropes. The setup is shown below. 80 kg are dropped from a height of 4.8 m in a guided fall setup. There are 2.8 m of rope available to catch the fall creating a fall factor of roughly 1.7. The fall is redirected over a relatively dull edge with a radius of 5 mm (here shown as a carabiner). Usually in this test setup a dynamic rope gets tested for their dynamic elongation and their impact force (both measured on the first fall) as well as for their maximum number of falls until they fail [3].
The UIAA sharp edge test replaced the edge in this test setup with a special edge that had mainly measurement specific definitions. The most important one of them being a "sharp" radius of 0.75 mm. The test then was conducted by the same fall specified in EN 892/ UIAA 101. If the rope held at least one fall the rope could be labelled as "UIAA Sharp Edge Resistant" [4].
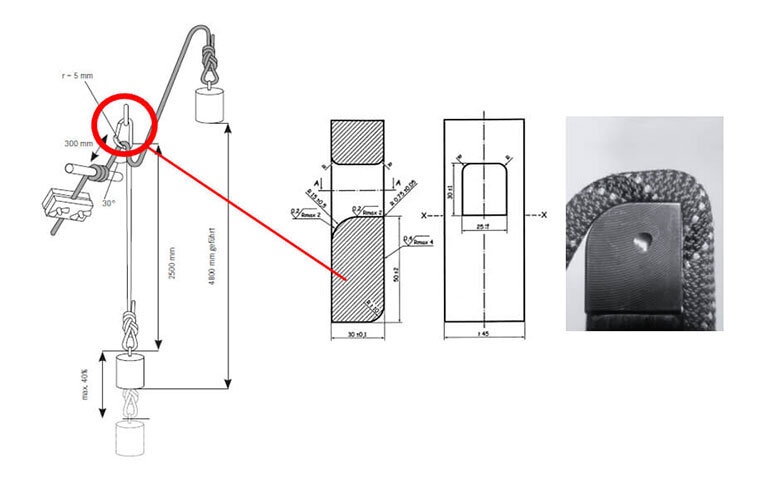
Long story short: the test got suspended after less than two years in 2004, because of a lack in reliability. Reliability is the key characteristic a test has to have in order to become standardized. Test results need to be consistent. So whenever the test is done and whoever does the test he or she should come to the same results. This was not the case for this test and the reasons for it might sound simple but poses the general challenge of the quest of finding a standardized test for cut resistance. Basically the test failed because of two reasons:
- An edge will get dull over times. This means that you cannot determine if a test result is as good/bad because you are testing a truly good/ bad rope or if your edge is not/ still sharp. This could have been partly solved by specifying the material of the edge very precisely and/ or introduce a reference rope that will always deliver the same results given a minimum sharpness. Neither of this was specified in the standard.
- A dynamic test setup will never create the same fall twice. A dynamic test setup might seem more "realistic", but this is not the main objective when trying to have a standardized test. In this case it matters a lot how a rope gets loaded over the edge, e.g. it might travel a bit more sideways over the edge in one fall compared to the next fall.
What started with a marketing initiative of a manufacturer at the time proved to be just that after 2004.
2004 - 2011: Further proposals and discussions
In the time after the suspension of UIAA 108 there were a couple of proposals and new discussions about how to tackle the need for a quantifiable method to judge the cut resistance of ropes. From the work of Blümel, Senner & Baier (2007) "Development of a sharp edge resistance test for mountaineering ropes" over the proposed Traverse Edge Test of Radek Fáborský to further static tests proposed in the UIAA committee. Each and every test finally did not come to an acceptable level of reliability and/ or usefully comparable test results.
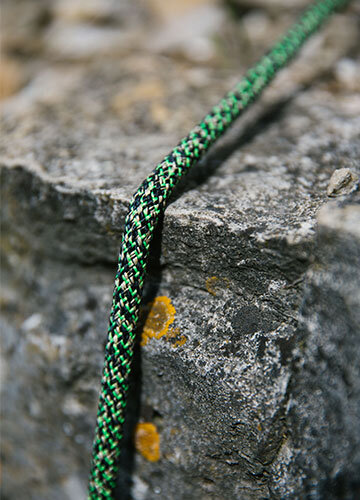
In the end the importance of the topic and the need to reliably quantify and compare the cut resistance of ropes remains the same: We learned that sharp edges are the biggest threat to our ropes and therefore a huge threat to our safety. However, our choice which rope we use or buy today can only be based upon manufacturers data that basically do not tell us anything about this important safety characteristic. According to the European Standard for dynamic Ropes EN 892 manufacturers have to supply the following information about the performance of their product:
- Rope Type: Single Rope, Half Rope, Twin Rope
- Diameter
- Weight per meter
- Number of falls
- Static elongation
- Dynamic elongation
- Impact force
- Sheath-/core proportion
- Sheath slippage
Some of the provided data can help you to find a good fit for your endeavor. Weight for example can obviously be crucial. But what does it tell you about how safe your rope is? Nothing! The only characteristic you could argue about is maybe the number of falls. However, never since 1963 was an accident recorded where a rope failed due to too many taken falls. This of course also is due to the fact that the falls measured are loads that may never occur in a real life situation. You could see number of falls therefore as a good measurement to differentiate a static rope from a dynamic rope – nothing really more.
If we could find a way to measure cut resistance of ropes, we might be able to describe a characteristic for ropes that actually matters in terms of safety!
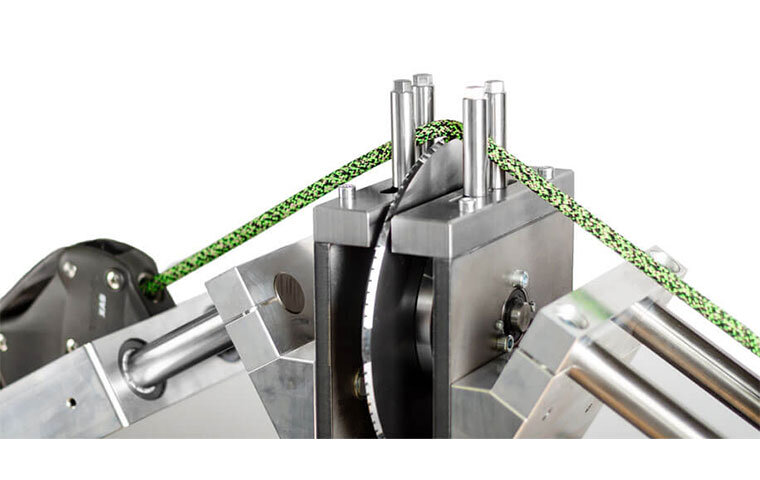
THE BIGGER, THE BETTER?
Imagine the two following hypothetical scenarios:
Scenario 1: You are walking over a glacier in a party of three using a 10.0 mm single rope. You reach a place where you have to abseil for a few meters over rocky terrain exposing your rope potentially to some rock edges. To save time you decide to lower two people with said rope at the same time after which the third person rappels by herself. A few minutes later you find yourself dangling with your friend midair 10 m off the ground, hanging off the 10.0 mm single rope.
Scenario 2: You are on the same tour with both of your friends. This time only, you have decided to go light and take an 8.9 mm triple-certified single rope with you. You again reach the abseil spot, but this time decide to lower two persons one after another until the third one rappels by herself. This time you find yourself dangling alone midair 10 m off the ground, hanging off an 8.9 mm single rope.
At this point, I ask you the following question: In which of these scenarios do you imagine yourself feeling more comfortable?
From my experiences confronting people with this story and questions many including recent myself would have answered the first question with: "scenario 1". But which of these scenarios is objectively safer?
Motivation
The first scenario is built upon a real accident that happened in 2015 during a training of the Swiss mountain guide association. Two people were lowered at the same time on an 8.7 mm single rope. The loaded rope got cut after sliding sideways for a few centimeters on a rocky edge. Both young mountaineers luckily survived the fall. The discussion that erupted afterward was based on the emotionally understandable demand to, therefore, use thicker ropes in the future and started a long process of cut resistance research here at EDELRID in the first place. Now with a reproducible testing method in place, we can look at this specific matter in more detail.
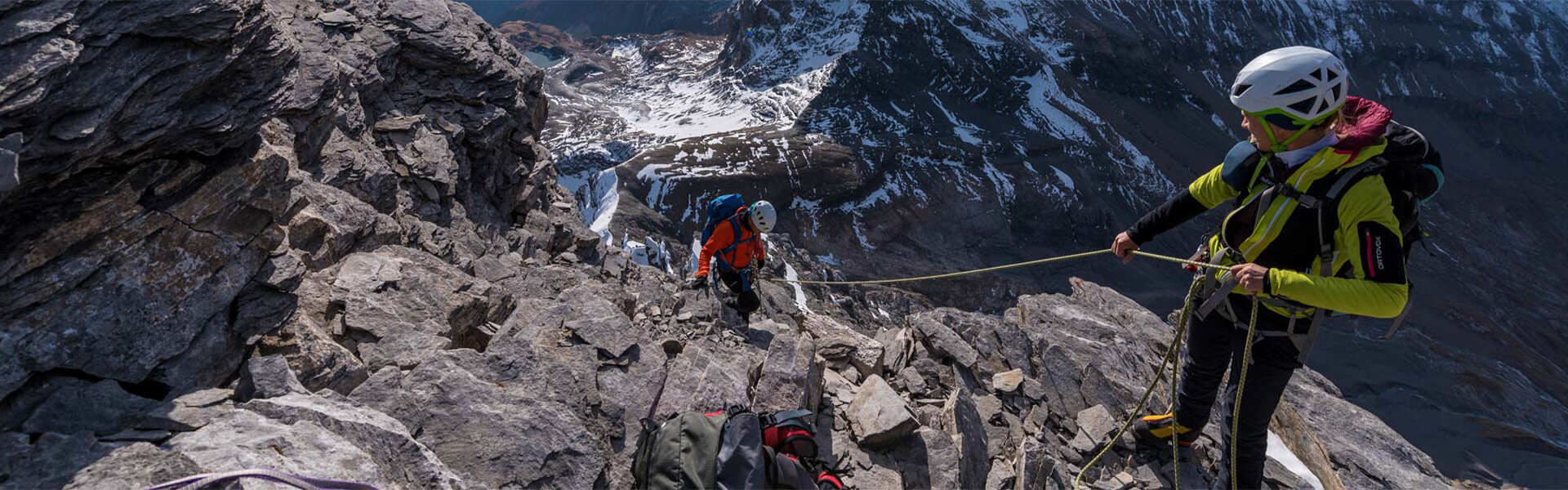
Subject of research
The specific question that we seek to answer in this episode is the following:
Which circumstances have bigger safety reserves in terms of cut resistance:
- thick rope diameter (e.g. 10.0 mm) and heavy load (e.g. 160 kg = two climbers)
- thin rope diameter (e.g. 8.9 mm) and lighter load (e.g. 80 kg = one climber)
And with the answers we get, we will be able to return to the scenarios described above in the introduction and look at the question: Which of the two scenarios are objectively safer?
Remember that in the bigger picture of this series we try to find out what influences the cut resistance of rope systems. So with the results, we further can hope for some evidence about the influences of diameter and load within a rope system. If you want to find out more about the mentioned testing method here, check out the first article of this series.
Test Setup
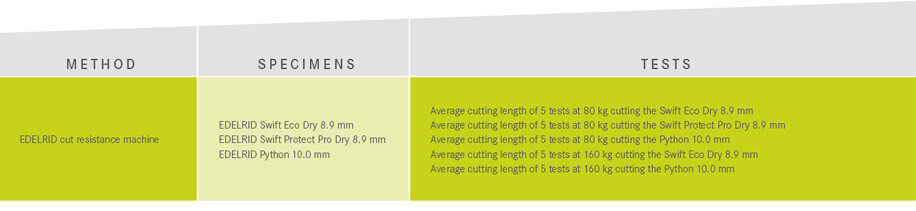
Results
The summed up results of the five different testing setups are shown here:
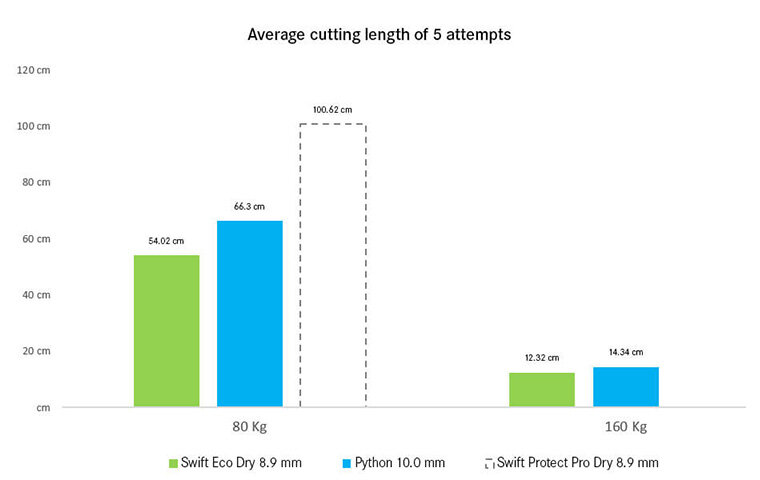
These results show a few very interesting points: Let's look at the average cutting lengths of the two different EDELRID ropes Swift Eco Dry 8.9 mm and the Python 10.0 mm loaded each time with 80 kg – trying to resemble the load of one person. We see that the 10.0 mm rope achieves a higher value than the 8.9 mm rope (22.7 % higher). Also shown here are the results cutting the EDELRID Swift Protect Pro Dry 8.9 mm rope at 80 kg of load, resulting in a much higher cutting length than both other ropes.
If the load is now increased to 160 kg resembling the weight of two persons we see a dramatic drop of the cutting lengths of both ropes (-77.2 % for the 8.9 mm rope and -78.4 % for the 10.0 mm rope). We also see that given the load of 160 kg the difference between both diameters is only 16.4 %.
Remarks on the results
Please have in mind that these results are laboratory results measured on a specific testing machine and set up that was built in order to get reliable, reproducible and therefore comparable results. Similar to the number of standard falls provided in the technical data of your dynamic rope, these values do not correspond to practical performances in real-life applications. However, the machine we designed to test the cut resistance on achieves results with reproducibility and reliability that has to our knowledge never been achieved before and are therefore the best way to get indications for safety-relevant questions.
Interpretation
Looking only at the results of the 8.9 mm rope compared to the 10.0 mm rope at 80 kg, one could initially assume what one might intuitively expect: a larger diameter provides greater safety in terms of cut resistance. Without first going into detail about our second parameter to be investigated, we can also see the result for a very new and special rope that is tuned to cut resistance – The Swift Protect Pro Dry 8.9 mm. It shows a significantly higher cut resistance than both other rope and only this, unfortunately, proves already that the parameter diameter might not be a good indicator alone to judge the overall safety of a rope system regarding its cut resistance.
But back to our initial research goal to compare the influence of diameter against the influence of the involved weight. With both shown results of the test comparing the two diameters at 80 kg and at 160 kg we can now put the two scenarios described in the introduction into perspective:
If we take the rope system of a small diameter like 8.9 mm loaded only with 80 kg (one person) and compare its cut resistance with a rope system with a 10.0 mm rope but loaded with 160 kg we get a very interesting and obvious result:
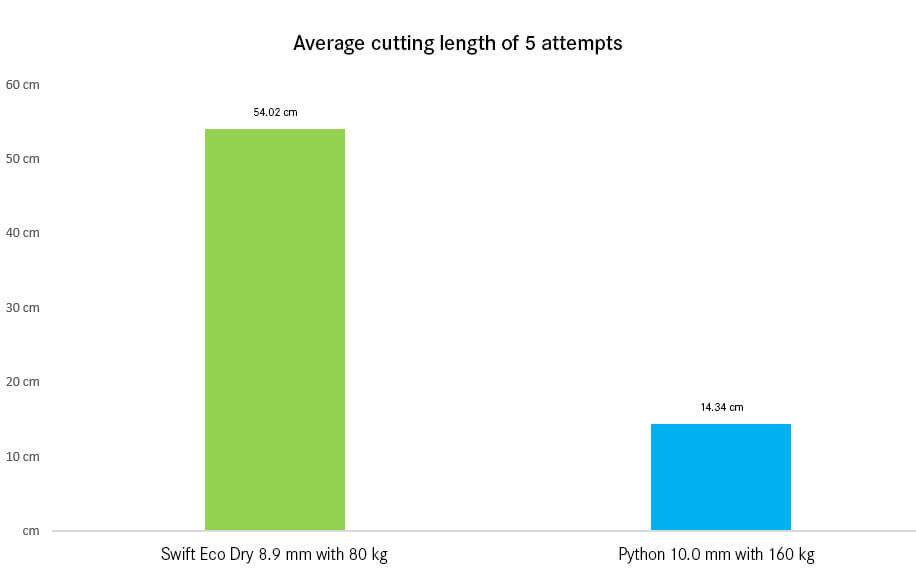
The first system in this example is 3.8 times more cut resistant! So it seems like the involved weight in a ropes system is much more crucial than the used diameter. With an increased diameter I might be able to also increase overall safety regarding cut resistance only when little weight is involved. As soon as the weight gets significantly high changing the diameter will not increase the overall safety significantly.
Conclusion
The overall conclusion here is simple and quite obvious. In order to increase the overall safety regarding cut resistance of a given rope system, one should try to reduce the weight that is applied within the system before looking for any other solutions! Examples here are lowering only one person at a time, using double rope techniques to reduce rope friction or dynamically belaying the climber to reduce the impact force in case of a fall.
This test also gives us another clue that will be elaborated in future episodes: diameter alone only increases cut resistance given a similar rope construction. As the user usually cannot judge a given rope construction, the diameter should not be a characteristic you should rely on to judge the cut resistance of your rope system.
Other rope properties and their influence on cut resistance
In the previous episode of this little series about cut resistance we learned that the diameter alone does not reliably inform us about how cut resistant a rope is. The question now stands: Does any other information provided with a rope give a useful indication about its cut resistance? Because, how else can a user make an informed choice of equipment to counter the verifiably major risk for ropes failing? In this episode we explore other characteristics of ropes and see if these give hints about a rope’s cut resistance.
If we do not find any answers here, this means two things: Firstly, this would mean that different cutting resistances of different ropes are then caused by the different rope constructions, which a user cannot possibly detect in every detail. And it means that it is about time that a suitable test is introduced that allows a reproducible way to measure this characteristic and informs the user accordingly.